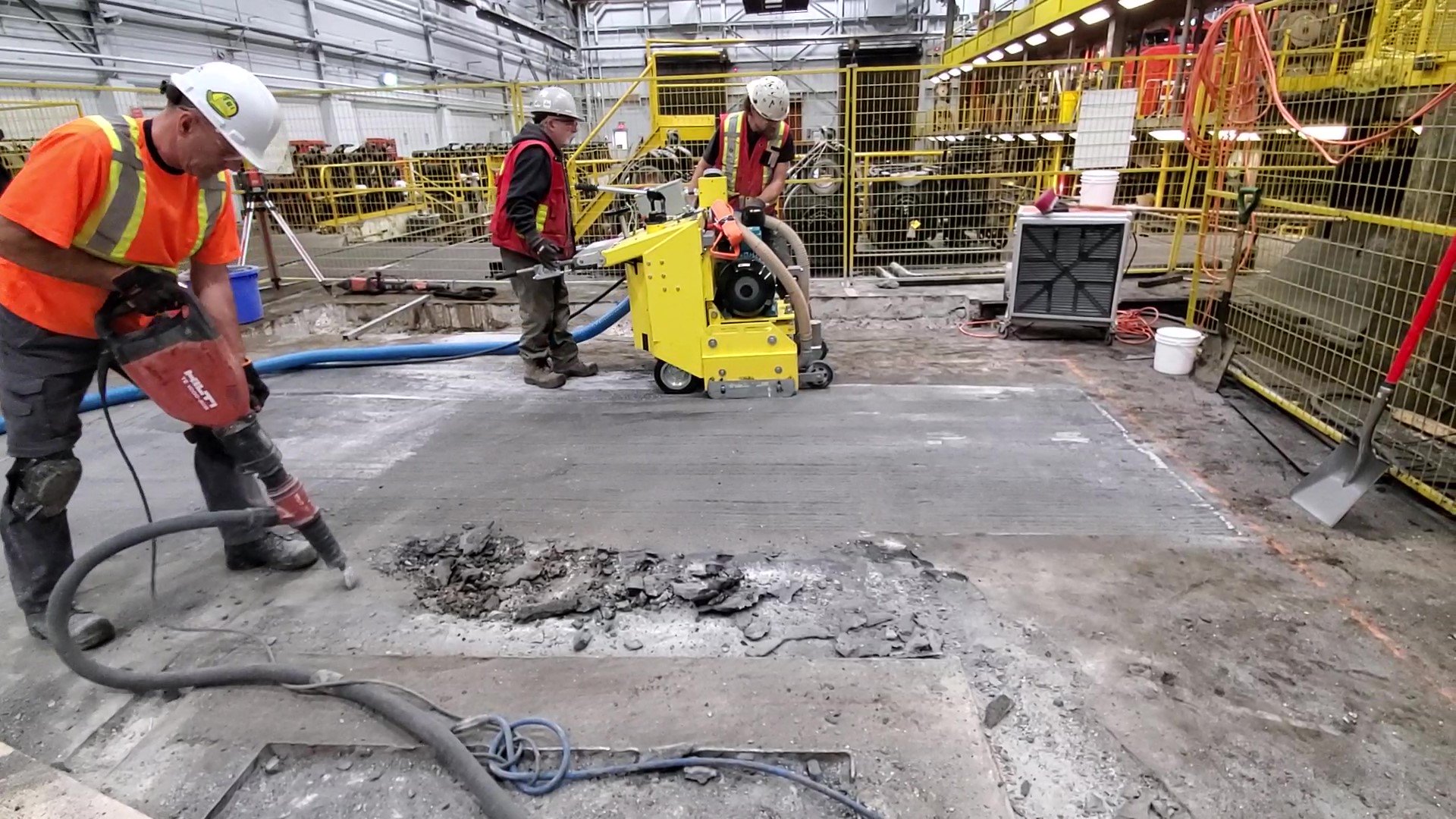
railway TRACK MOTOR repair work station
scope: demolish, de-contaminate, drain sump construction, concrete replacement, anti slip floor all using silikal(r) mma resins
Project Date: 2018
Facility: Eastern Canada
sloped floor, drain sump, anti slip floor
for heavy motor repair
problem definition:
EXISTING EPOXY / URETHANE HAD FAILED IN ABOUT 2-3 MONTHS. BETTER, PROVEN OPTION NEEDED.
FAST RETURN-TO-SERVICE REQUIRED. CANNOT SHUTDOWN CRITICAL MAINTENANCE FACILITY FOR EXTENDED PERIOD OF TIME USING CEMENTITIOUS CONCRETE, ALLOW FOR 28 DAYS CURING, AND THEN INSTALL FINISHED FLOOR.
DEMOLITION OF ENTIRE SLAB, RE-SLOPING WITH NEW SLAB, NEW TRENCH DRAINAGE FACILITY: 5-6 WEEKS
REPAIR / RENOVATE WAS FASTER THAN REPLACE BETTER AT 11 DAYS.
WATER AND OIL NOT DRAINING ACCUMULATING IN THE WORK AREA.
SLIPPERY ENVIRONMENT
NO DRAIN SUMP LOCATED ON THE FLOOR. NEW SUMP AND DRAIN REQUIRED
NEED TO DEMO / ACCOMODATE PREVIOUS CRANE SUPPORT IN MIDDLE OF WORK AREA.
UNDERGROUND IN / OUT PIPING NEEDED TO BE INSTALLED
IMPROVE HOUSEKEEPING. EASIER TO CLEAN FLOOR NEEDED.
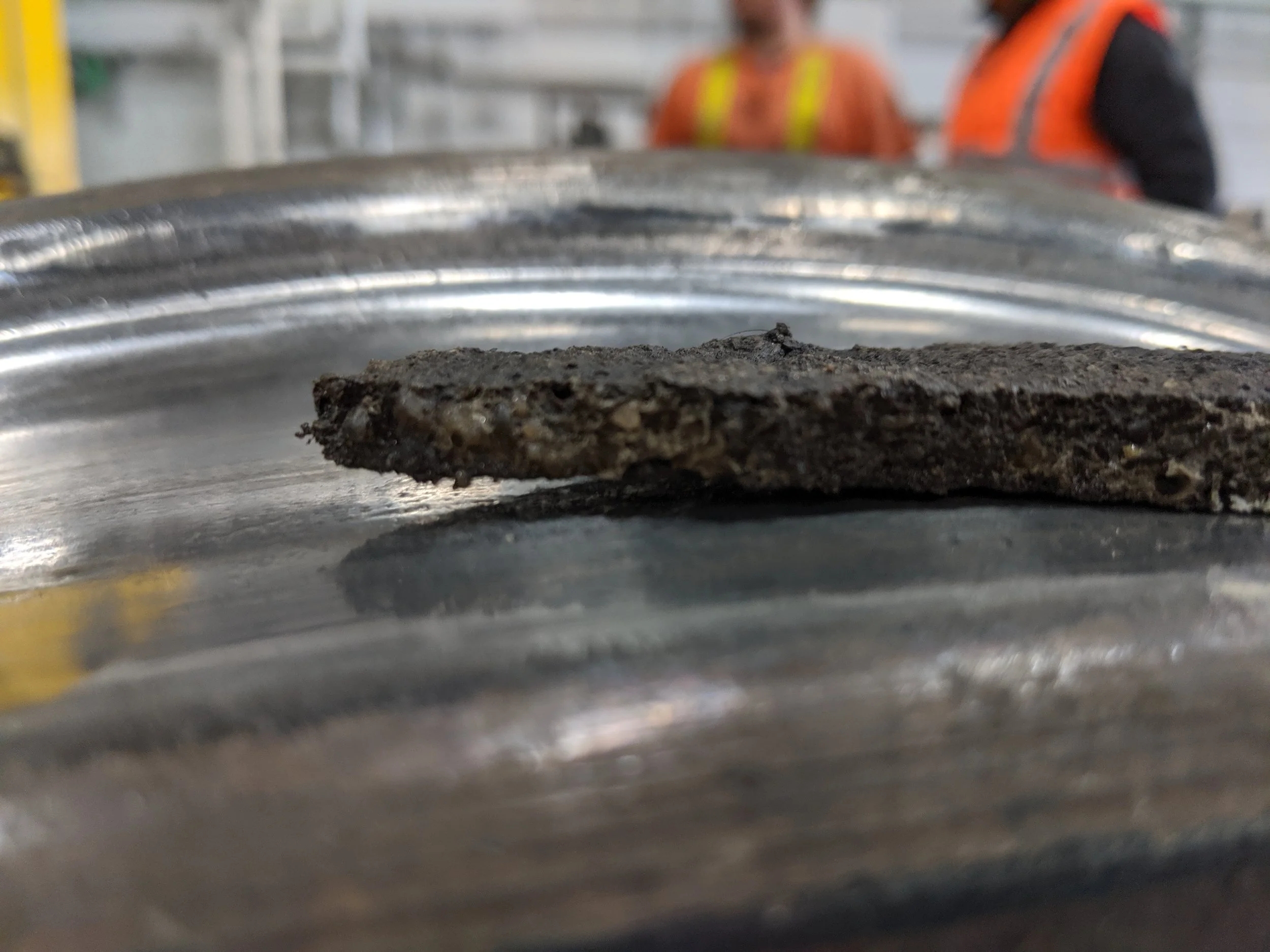
Previous resin floor failed in less than 3 months. SureBond had to remove about 25mm of oil contaminated material, and then prepare / de-contaminate the slab just to start the re-build work.
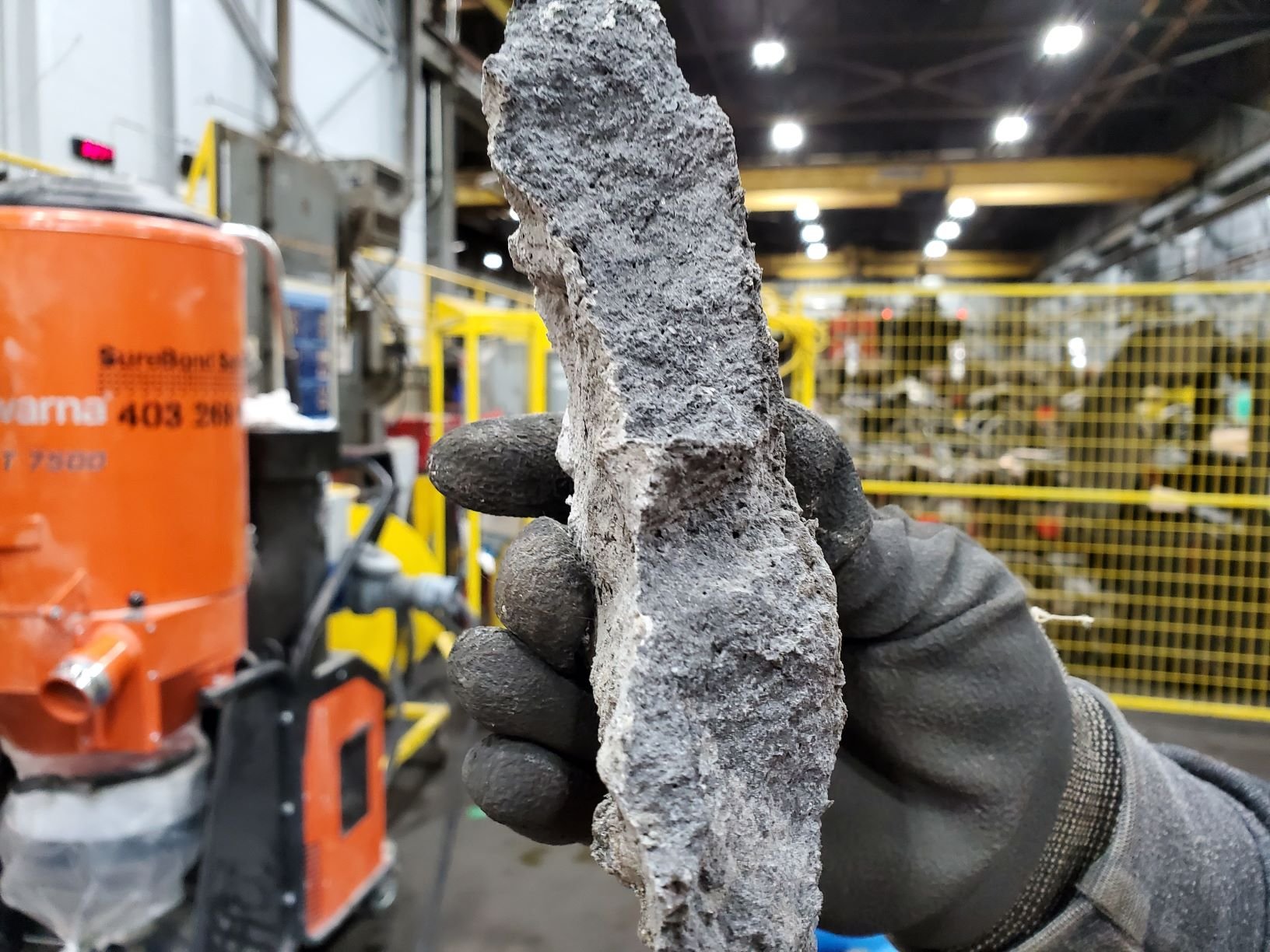
Additional concrete that had failed and needed to be demolished / replaced.

SureBond can safely demolish all concrete, failed epoxies /urethane cement materials with zero silica dust. We have unique prep equipment for all floor demolition. All equipment are tied to HEPA11 vacuum systems.

Much hand demolition around sub-surface steel work had to occur.
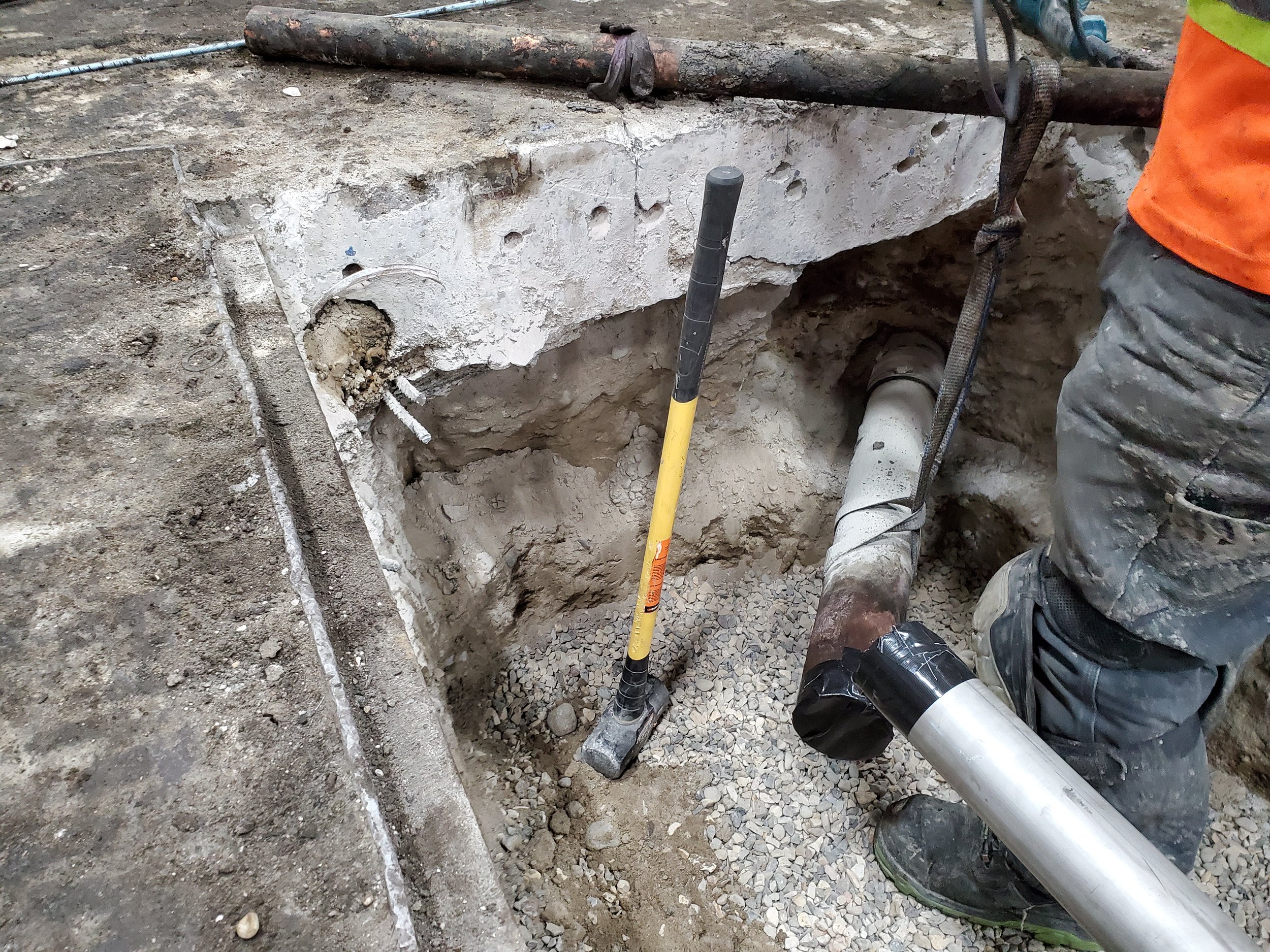
The start of our work was to build a sump for oil / water to drain into a oily sewer recovery system. We started with a hole in the slab / ground created by a local contractor. Drain pipes in and overflow out pipes penetrated into the hole. No box / sump assembly could be pre-built. We had to just field-fit the construction to accomplish the project goals.

Detailed cribbing of the new sump, and accommodating the in / out oily water piping.
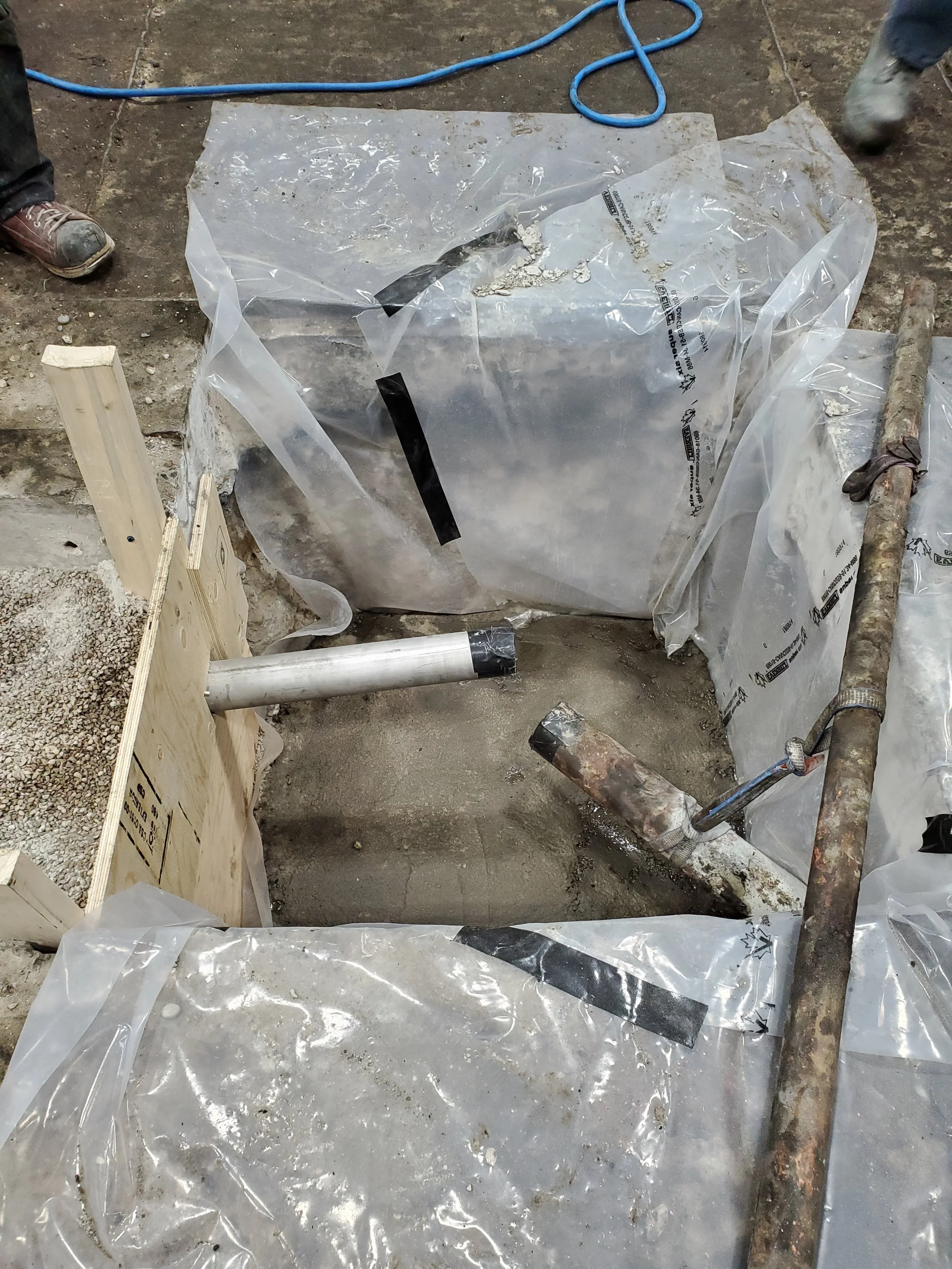
Isolation poly to keep our plastic R17 concrete resin away from sub slab soil.
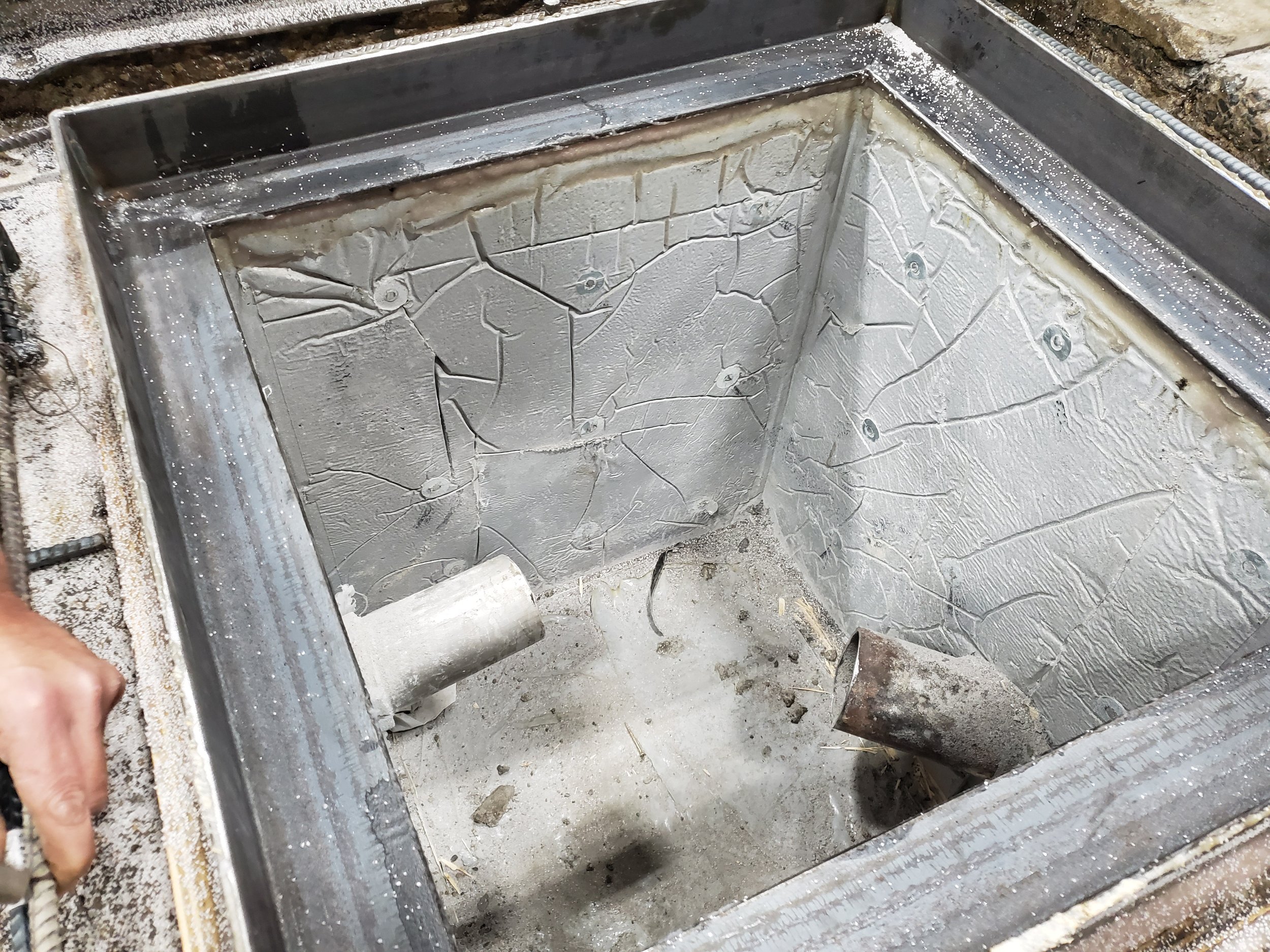
The cribbed box after pouring the Silikal R17 MMA plastic concrete resin with aggregate. Estimated strength at 85 MPa. Lines shown in the resin are the polyethylene as a bond breaker against the outside of the cribbing forms.
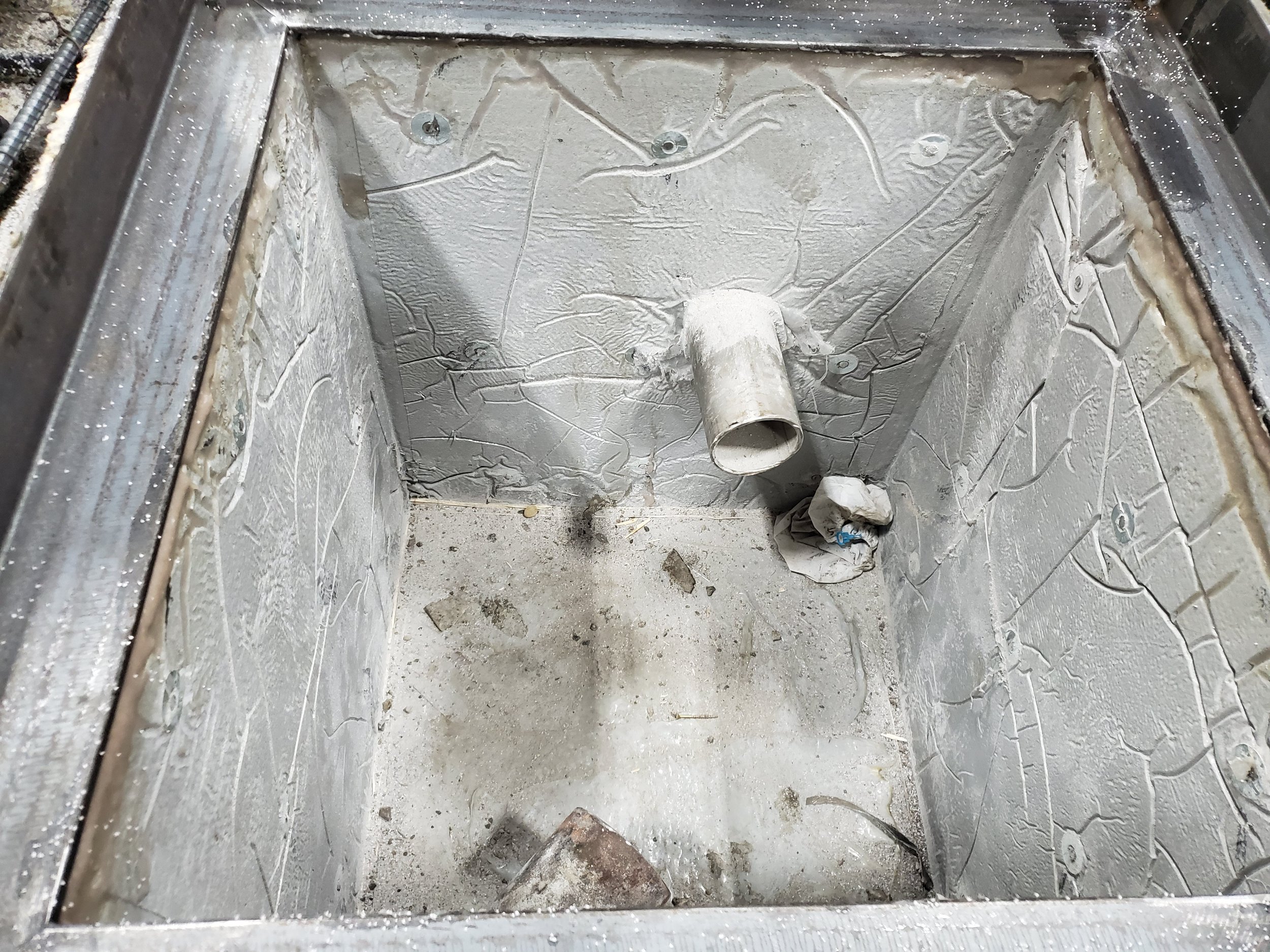
Another view of the completely water-tight, oil tight box. A Silikal R71 protective sealer was applied to all R17 surfaces to ensure that it would not be contaminated by oil from the track motor drainage going forward.
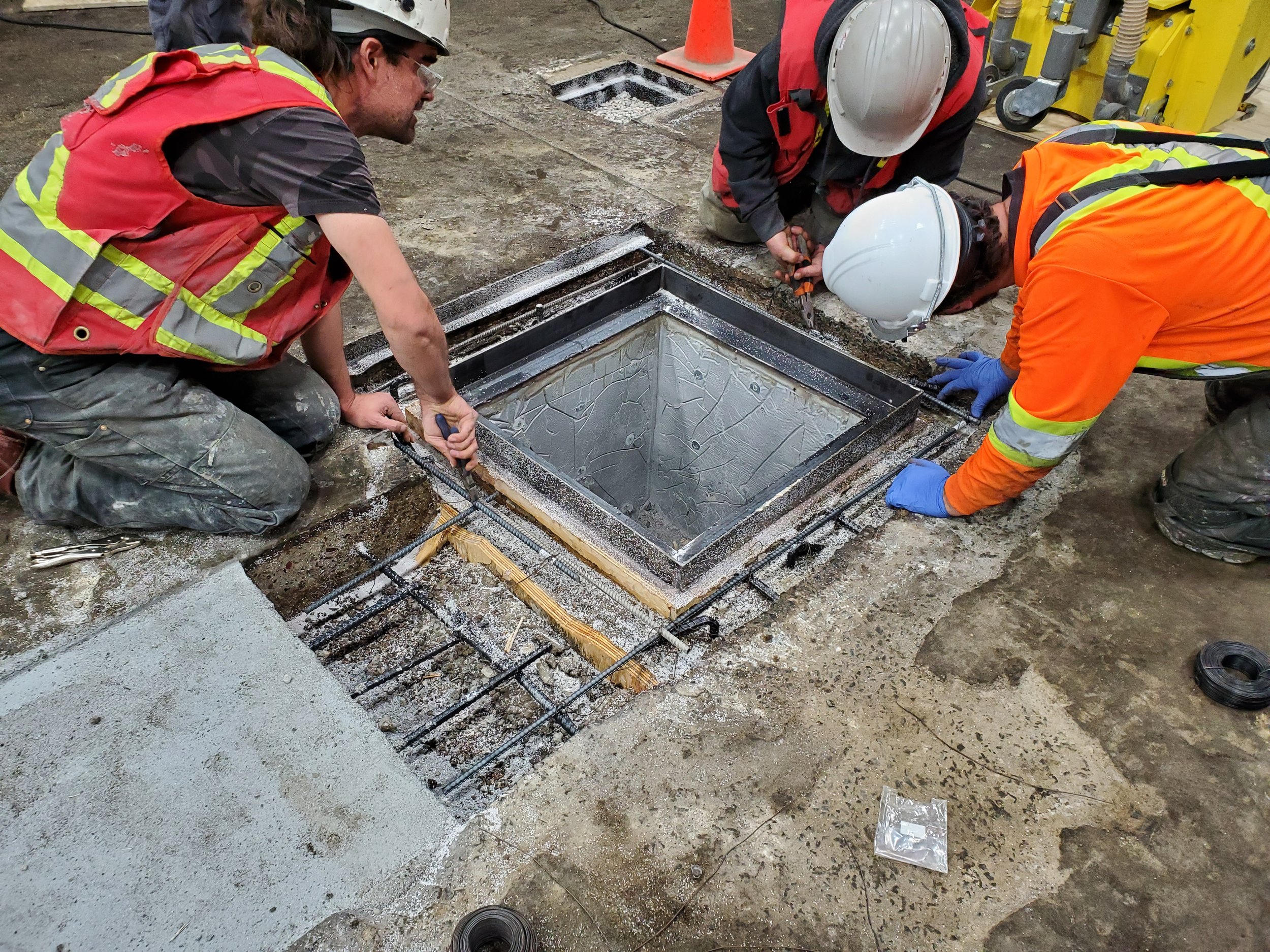
Steel rebar tied in around the drain sump before pour / fill with Silikal(r) R17.

Tying the pipe trench fill on the left to the drain sump on the right.
SureBond Complete. 11 days on-site. If this project had involved concrete replacement with a typical epoxy floor, this would have been 5-6 weeks duration with the same result. After all slab repair work was complete, we sloped the floor and installed the work surface Silikal R61 anti slip floor. The drain cover was added by the local contractor after SureBond completed this phase.
At 12 months service. And this is life on the track motor floor. Equpment weighing 10,000 to 14,000 lbs placed on the floor...but was supposed to have 1" plywood underneath to protect the floor.
At 12 months service. Great drainage. Dry work area has improved and brightened the work environment tremendously, as well as supplying a floor that is much easier to clean...
Floor at 12 month service.
Trades do not like working in a mess. This is their office. Our SureBond floor is not a finish in architectural terms. It is a work surface. It is fit-for-service defined by the railway client.
12 months service. A busy, safe work area.
12 months service Drain area was surrounded and now hidden from sub-surface structural steel. We were able to finesse the slope to cover over top of the unmovable steel structural, and bonding to the steel as well. No failure after 1 year.
12 months service. A tough work area. Wheel sets are rolled across the floor as well....unprotected. This will cause pre-mature wear...but the SureBond Silikal(r) floor IS repairable with a simple overlay at any point. Repairable, forever, without demolition and starting over from base concrete.
12 months service. Lots of oil, chemical, solvents are hitting this floor. A bit dirty, but not a priority. Anti slip, dry, and no peeling.
20 months service, just BEFORE cleaning of the floor. It's a tough world when working for the railway.

After CLEANING at 20 months service. Taken the next day after cleaning. This is how the floor be restored even after being left dirty for the entire duration of 20 months. An amazing improvement in the floor brightness. No peeling, even with impact and unprotected equipment moved / placed left on the floor. But, no peeling!
Quickly, the wheeled traffic gets the floor dirty. That's life. Cleaning more frequently would result in a easier to clean surface. But, the client is happy with the anti slip, drainage performance of the floor and the drainage provide.